8D Method for Effective Problem Solving
The Eight Discipline (8D) is a structured problem-solving method designed to identify, correct, and eliminate recurring issues through a team-based approach. Developed by Ford in 1987, it uses analytical tools and cross-functional collaboration to address complex problems across industries such as manufacturing, healthcare, and aerospace. The 8D method tackles three types of problems: immediate, gradual, and since inception, focusing on solving recurring complexities with the involvement of the entire team.
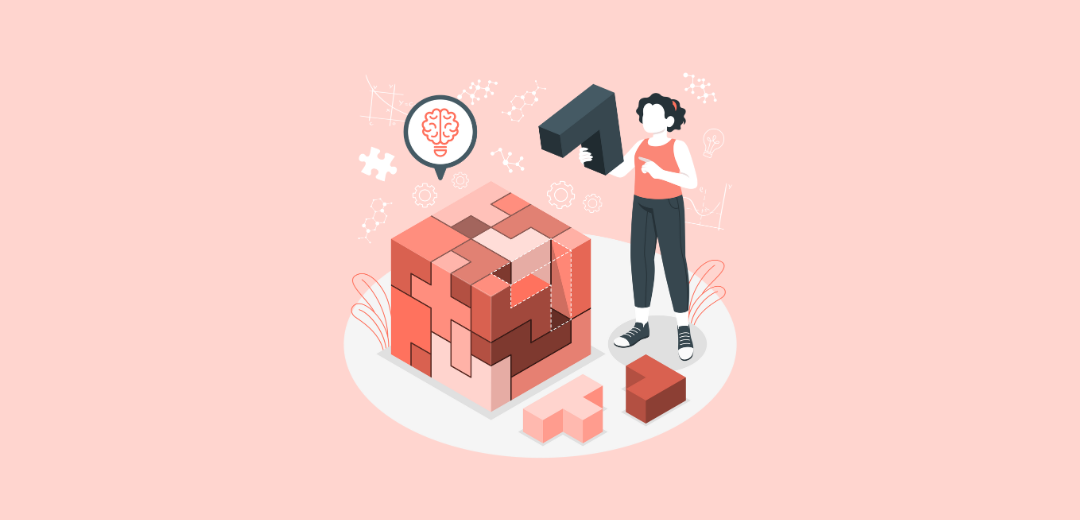
Managing a company is filled with challenges. But the important part is to find and address those challenges at the right time. Fortunately, some issues can be corrected immediately; others require more research. However, some persistent issues keep recurring.
In such situations, businesses use the popular 8D method for investigation and root cause analysis. 8D, as in “Eight Disciplines,” is a problem-solving method commonly found in automotive and other manufacturing industries.
In this article, we will discuss the 8D method of problem-solving in detail and explore its benefits. So if you ran across a problem that’s causing you a headache, then read till the end to get the most out of this 8D technique.
What is the 8D Problem-Solving Method?
The Eight Discipline (8D) is a problem-solving technique for identifying, correcting, and eliminating recurring problems. It is a structured, team-based approach to problem-solving. It also includes a detailed framework combining analytical tools, cross-functional collaboration, and a disciplined mindset to solve complex problems.
The concept was invented by Ford Motor Company in 1987. Initially, it was named TOPS (Team-Oriented Problem Solving), developed to solve recurring quality issues in the automotive industry at that time.
Soon, the 8D method became popular within Ford and was adopted as the company’s primary approach for documenting and addressing problem-solving efforts. Today, this method is being used across all sectors like manufacturing, healthcare, aerospace, and other service industries.
But what is the problem here that 8D solves?
According to 8D, a problem is any deviation from the set goal, which can be of three types:
- An immediate deviation: The issue emerges suddenly without any notice.
- Gradual Deviation: The issue appears over time, mostly as performance slowly worsens.
- Since Inception: Since a process or product life cycle began, the issue has been around but might not have been instantly recognized.
Basically, any recurring complexity in the workflow that demands the involvement of the entire team to resolve is solved through the 8D technique.
How to Apply the 8D Problem-Solving Method?
8D for investigation is a systematic process of improving business workflow and team productivity. The technique focuses on eight stages to investigate an issue’s root cause and how to solve it. It is a team-based approach that helps organizations address concerns and prevent future problems.
So, let’s say you have a manufacturing company that produces plastic components for automotive dashboards. Recently, you have been experiencing a surge in customer complaints about surface scratches on the component. You decided to do an 8D to investigate the problem.
Here’s what an entire process will look like:
1. D0: Preparing a Plan
When you notice an increase in customer complaints about scratched components, you begin by logging the issues and communicating with management. You create a plan to assess each stage of the manufacturing process to identify potential root causes.
2. D1: Establish the Team
You form a cross-functional team to tackle the issue, which includes quality control engineers, production line operators, materials specialists, and customer service representatives. You appoint a team leader and clearly define roles and responsibilities to ensure smooth problem resolution.
3. D2: Describe the Problem
You define the problem as increased customer complaints about visible scratches on dashboard plastic components, leading to a 15% rise in returns. You gather data, such as the frequency and location of the scratches on the components and the production dates of the affected items. This helps you understand the scope of the issue and identify any patterns.
4. D3: Develop Interim Containment Plan
To limit further customer dissatisfaction, you implement interim containment actions. These include conducting more frequent inspections of the finished components before shipment and using protective wrapping during transportation.
5. D4: Determine and Verify Root Causes and Escape Points
You investigate the root cause using tools like the “5 Whys” analysis and fishbone diagrams. After a thorough analysis, you discover that a specific section of the convey or belt in the production line has developed a rough surface, causing the scratches.
The 5 Whys is a simple method for finding the root cause of any problem by asking, “Why?”For example:
- Why are there scratches on the dashboard components?
- Why does the conveyor belt have rough spots?
- Why hasn’t the belt been replaced?
- Why was the maintenance schedule insufficient?
- Why wasn’t there an inspection process in place?
The Fishbone Diagram, also called the Ishikawa diagram and cause-and-effect diagram, is a visual tool that identifies, explores, and displays the possible causes of a particular problem. It resembles a fish’s skeleton, where the head represents the problem and the bones represent various categories of potential causes, such as materials, methods, machines, manpower, and environment. In your case, the rough conveyor belt surface would fall under “Machines” in the diagram.
6. D5: Verify Permanent Corrections
You explore potential permanent solutions to fix the issue, such as replacing the damaged section of the conveyor belt, applying a protective coating to it, or changing the material of the belt. After testing, you determine that replacing the damaged section with a new, smoother conveyor belt is the best solution, as it eliminates the scratches.
7. D6: Define and Implement Corrective Actions
You define and implement corrective actions, including installing the new conveyor belt and closely monitoring the production line to ensure no further scratches occur. Additionally, you improve the quality check process to better detect any defects in the future.
8. D7: Prevent Recurrence
To prevent the issue from happening again, you implement preventive measures, such as regular inspections of the conveyor belt and a scheduled preventive maintenance plan for the production line. You also update quality control procedures and train staff on the new inspection and maintenance protocols.
9. D8: Recognize and Congratulate the Team
Finally, you communicate the improvements to the rest of the company and document the lessons learned for future reference. Recognizing the team’s effort not only motivates them but also reinforces the importance of proactive problem-solving in maintaining product quality.
Timeline of the 8D Process
The 8D process should be both thorough and timely. However, the duration of each step can vary depending on the complexity of the problem. Typically, the process follows a structured timeline:
- The team should complete D1 and D2 (team formation and problem definition) within 2 days, along with initial containment actions (D3).
- The team should finish the root cause analysis (D4) within 7 days and update the 8D report with its findings.
- The team should define corrective actions (D5) and outline implementation steps (D6) within 14 days.
- The team should finalize the entire 8D report, including verification of corrective actions and preventive measures, within 60 days.
Root Cause Analysis Tools in 8D
Root Cause Analysis (RCA) is an important step in the 8D technique because it makes sure that the problem is solved at its core. If the underlying issue isn’t addressed, temporary fixes or surface-level solutions will only provide short-term relief while the problem continues to affect quality, customer satisfaction, and costs. Root cause identification helps implement long-lasting corrective actions, ensures that the issue doesn’t resurface, and improves overall operational efficiency.
For RCA, teams can use various tools depending on the complexity and nature of the problem, like:
5 Whys
The 5 Whys technique is a straightforward, iterative approach to identify the underlying cause of a problem. By asking “Why?” five times (or as many times as needed), you dig deeper into the problem. This helps one to find the underlying cause, getting past the symptoms. If, for instance, scratches on parts are the problem, asking why they happen often reveals issues, including equipment wear, inadequate upkeep schedules, or defective examination procedures.
Ishikawa (Fishbone) Diagrams
The Ishikawa diagram is a visual tool that helps categorize and explore potential causes of a problem. It breaks down the investigation into several categories, such as materials, methods, machines, manpower, and environment, which can lead to more structured thinking. The diagram helps identify where the problem may stem from, whether it’s a machine malfunction, human error, faulty materials, or external factors, enabling a more comprehensive analysis.
Fault Tree Analysis (FTA)
Fault Tree Analysis is a top-down approach used to identify the root cause by modeling the problem and tracing how different events or failures contribute to the overall failure. Starting from the top event (the problem), the analysis breaks down the system into a tree structure of possible contributing factors, leading to root causes. FTA is especially useful in complex systems where multiple factors interact to create a failure. This tool helps identify how various system components, both technical and human, contribute to the failure, making it easier to pinpoint the exact cause.
These tools provide both a structured and visual approach to identifying the root cause so that no potential contributing factor is overlooked.
Read: Workplace Incident Management: Key Steps and Tools
Benefits of the 8D Methodology
The 8D approach offers several key benefits:
- Structured Problem Solving: Gives a clear, step-by-step strategy for logically handling issues, thereby guaranteeing no important detail is overlooked.
- Root Cause Identification: This approach helps find the root cause of problems, offering lasting solutions rather than simply treating symptoms.
- Cross-Functional Collaboration: This promotes teamwork across departments and uses several areas of knowledge to develop better solutions.
- Prevention of Future Problems: Emphasize corrective and preventive actions, increasing their probability of not happening.
- Continuous Improvement: Encourages a company to constantly improve its workflow, helping it remain competitive and changeable.
- Improved Product Quality & Customer Satisfaction: Better product quality reduces complaints, leading to higher customer satisfaction.
- Documentation & Accountability: Ensures clear tracking of actions taken, providing valuable insights for future improvements and ensuring accountability.
Challenges and Pitfalls in 8D Methodology
While the 8D methodology offers many benefits, it also presents challenges:
- The process can be lengthy, especially for complex problems, causing delays in resolution.
- Requires dedicated cross-functional teams, which can strain resources.
- Teams may resist new procedures, hindering implementation.
- Incorrect or incomplete data can lead to ineffective solutions.
- Applying 8D to simple problems can waste time and resources.
- A lack of clear communication can cause misunderstandings and delays.
- Incomplete implementation of corrective actions can lead to recurring problems.
- Focusing too much on long-term solutions can delay immediate fixes.
Case Studies and Applications of 8D Methodology
Let’s look at some real-world examples from different sectors to see how the 8D problem-solving approach can be applied practically to resolve issues.
1. Automotive Industry – Toyota’s Unintended Acceleration Recall (2009-2011)
In 2009-2011, Toyota faced a major recall of millions of vehicles due to unintended acceleration, which resulted in several accidents. The issue was traced to a faulty electronic throttle system and pedal design. Using the 8D methodology, Toyota identified the root cause, implemented corrective actions (e.g., redesigning pedals and reprogramming throttle systems), and improved quality control measures.
The 8D process helped Toyota resolve the issue, restore customer trust, and implement stricter safety protocols, preventing similar problems in future models.
2. Food Industry – Chipotle E. coli Outbreak (2015)
Chipotle experienced an E. coli outbreak in 2015 linked to several locations, resulting in hundreds of customers affected. The 8D methodology helped identify the root causes: faulty suppliers and improper food handling. Corrective actions included replacing suppliers, upgrading food safety protocols, and enhancing employee training.
The recall, along with improvements in food safety measures, reduced future incidents and helped restore the brand’s reputation.
3. Electronics Industry – Samsung Galaxy Note 7 Battery Explosions (2016)
Samsung recalled millions of Galaxy Note 7 smartphones in 2016 due to battery explosions. Using the 8D methodology, Samsung identified the root cause: defective batteries and implemented corrective actions such as redesigning the battery and improving quality control in production.
Although the recall caused financial loss, Samsung applied the 8D method to improve battery safety standards and regain consumer trust.
Read more: How to Assess and Analyze Risks in Business: Easy Steps to Follow
How VComply Can Enhance the 8D Technique?
The 8D methodology is a powerful tool for addressing complex quality issues, but it also comes with some challenges. From delays in case tracking to communication gaps and lack of real-time insights, these challenges can slow down the process.
VComply’s CaseOps platform provides a comprehensive solution to simplify the 8D methodology for root cause analysis (RCA) and resolve these common challenges.
Here’s how VComply can enhance each step of the 8D process:
- It simplifies case intake by enabling customizable forms and secure links for easy reporting.
- The platform centralizes all case-related data in one secure, accessible platform. This allows teams to store, track, and access crucial information in real-time.
- It automates task assignments, stage reviews, and notifications, ensuring that the 8D process flows smoothly.
- With intuitive dashboards, the VComply platform provides real-time monitoring of case status, overdue tasks, and progress updates.
- It also maintains comprehensive audit trails with detailed logs of every action taken in the 8D process.
Experience how CaseOps can streamline your 8D methodology. Request a demo today to see the platform in action.
Wrapping Up
The 8D methodology is a highly effective problem-solving tool that helps organizations address complex quality issues, identify root causes, and implement sustainable solutions. However, it comes with its own set of challenges, such as inefficient case intake processes, scattered information, manual task management, lack of real-time tracking, and difficulties in identifying trends for continuous improvement.
VComply, through its CaseOps platform, resolves these challenges by offering a streamlined, automated, and centralized system for managing the entire 8D process.
Request a 21-day free trial today and see how VComply can streamline your RCA efforts and improve your organization’s quality management practices.