Practical Guide on Conducting Safety Risk Assessments and Management
Safety risk assessments are essential for identifying and managing workplace hazards before they cause harm. They involve evaluating the likelihood and severity of potential risks to people, property, or the environment. Typically conducted by employers or safety professionals, these assessments help create a safer, more proactive work environment.
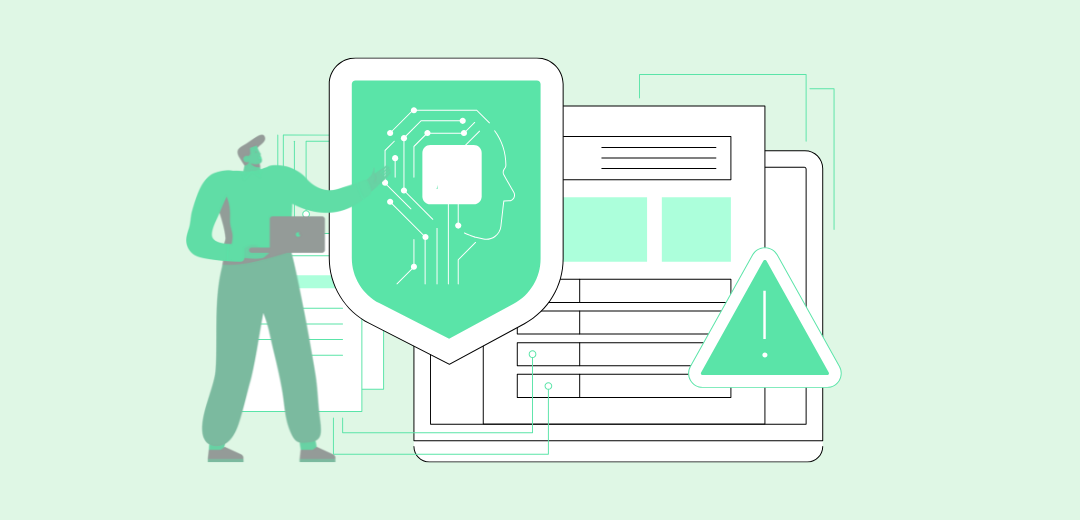
Every year, millions of people suffer serious harm at work. In fact, 18% of the global workforce, roughly 667 million adults, have experienced significant harm on the job in the last two years.
These incidents aren’t just numbers; they represent real people, real risks, and a major wake-up call for organizations everywhere.
So, how can we prevent such accidents from happening? It all starts with a safety risk assessment.
This blog will guide you through conducting safety risk assessments and managing risks effectively. We’ll cover the basics, step-by-step procedures, and practical tips to help you create a safer work environment.
What is Safety Risk Assessment?
Safety risk assessments are the foundation of a safe workplace. They provide a systematic way to identify and manage potential dangers.
Safety risk assessments are a crucial part of maintaining a safe workplace. They help organizations find and evaluate potential dangers before they cause harm.
To understand these assessments, it’s important to know some basic terms:
- Hazard: A potential source of harm, including injury, health effects, or damage. Hazards are often categorized as biological, chemical, ergonomic, physical, psychosocial, or safety-related.
- Risk: The combined likelihood and severity of harm occurring when exposed to a hazard, applying to people, property, or the environment. Risk is calculated by probability multiplied by severity.
- Likelihood (Probability): The chance or extent to which a harmful event is likely to occur.
- Severity (Consequence): The magnitude or seriousness of the potential harm from a hazard, described using terms like catastrophic, critical, moderate, or minor.
A safety risk assessment aims to determine the extent of potential harm in a given situation. The assessment defines the purpose and scope of the examination.
Responsibility for carrying out risk assessments typically falls to employers or designated safety professionals, but may also involve input from employees, supervisors, and external experts depending on the complexity and nature of the risks.
When to Conduct Safety Risk Assessments
Conducting safety risk assessments is not a one-time task; it is an ongoing process that various events and situations should trigger.
It is the employer’s responsibility to perform risk assessments when:
- New processes or steps are added to the workflow.
- Changes are made to existing processes, equipment, or tools.
- New hazards emerge due to changes in the work environment or other factors.
- Incidents or near misses occur.
Additionally, you perform risk assessments regularly to ensure controls remain effective and to update them as necessary.
Types of Risk Assessments
Risk assessments are tailored to the specific hazards and activities within a workplace. Rather than focusing solely on industry-specific assessments, it’s helpful to consider broader categories. These can include:
- General Health and Safety Risk Assessments: These assessments cover a wide range of common workplace hazards, such as slips, trips, falls, and ergonomic issues. They form the foundation of a safe working environment and are applicable across various industries.
- Hazard-Specific Risk Assessments: These assessments delve into particular hazards that pose a significant risk, such as those related to hazardous substances (e.g., COSHH), machinery operation, working at heights, or confined spaces.
- Activity-Specific Risk Assessments: These assessments focus on specific tasks or processes that may introduce hazards, such as manual handling, welding, or electrical work. They often result in detailed procedures or method statements (e.g., RAMS) to control the identified risks.
- Environmental Risk Assessments: These evaluate the potential environmental impact of workplace activities, including pollution, waste disposal, and resource consumption.
- Fire Safety Risk Assessments: Required in all workplaces, these assessments identify fire hazards, evaluate fire safety measures, and ensure adequate escape routes and emergency procedures.
- Display Screen Equipment (DSE) Assessments: These focus on the risks associated with prolonged use of computers and other display screens, addressing ergonomic factors and potential health issues.
The appropriate type of risk assessment will depend on the nature of the work being carried out, the hazards present, and any relevant legal requirements. Regularly reviewing and updating these assessments is crucial to maintaining a safe and healthy workplace.
Benefits of Conducting Safety Risk Assessments
Conducting safety risk assessments offers numerous benefits to organizations, enhancing both the safety and efficiency of the workplace. Here are some of the key advantages:
- Improved Safety: Risk assessments help identify and mitigate hazards, reducing the likelihood of accidents and injuries in the workplace. This proactive approach ensures a safer environment for employees and visitors.
- Increased Productivity: By understanding potential risks, employees can implement measures to mitigate them, leading to smoother operations and increased productivity. This awareness also helps handle unexpected events more effectively.
- Cost Savings: Implementing risk management strategies can reduce operational costs by minimizing the financial impact of unforeseen events. Additionally, preventing accidents can save on costs related to medical treatment, compensation, and legal liabilities.
- Enhanced Employee Awareness and Engagement: Risk assessments involve educating employees about hazards and control measures, fostering a culture of safety awareness and responsibility. This engagement can lead to better morale and retention.
- Compliance with Regulations: Risk assessments are often legally required to ensure employers are taking adequate steps to protect employees’ health and safety. Conducting these assessments demonstrates compliance with health and safety regulations, reducing the risk of fines and legal issues.
- Better Decision Making: Risk assessments provide valuable data that can inform strategic decisions about resource allocation and budgeting for safety measures. This helps organizations prioritize risks effectively and allocate resources accordingly
Now, let’s move on to how you can conduct one of these assessments step-by-step!
Also read: Retail Safety Training for Store Workers: A Comprehensive Guide
The Step-by-Step Process of Conducting a Safety Risk Assessment
Conducting a safety risk assessment involves a structured process to ensure thoroughness and accuracy. This process is typically broken down into several phases.
Step 1: Hazard Identification
To begin, we need to find all possible hazards in the workplace. This involves a thorough search for threats, such as:
- Physical hazards might include unguarded machinery, electrical risks, or fall hazards.
- Chemical hazards involve exposure to substances capable of causing harm, such as toxic fumes, corrosive materials, or flammable liquids.
- Biological hazards, such as bacteria, viruses, or other infectious agents, can lead to illness through exposure.
Effective hazard identification is achieved through regular workplace inspections, reviewing past incident reports meticulously, and direct consultation with employees.
Examination of manufacturer’s safety data sheets (SDS) for chemicals provides crucial information about potential risks.
It’s also essential to consider who might be affected by these hazards. This includes employees, contractors, visitors, and members of the public who may be present in or around the workplace.
Step 2: Risk Evaluation
Once hazards are identified, the next step is to evaluate the risks they pose. This involves determining the probability of an incident occurring, considering factors like frequency of exposure, existing safety measures, and past incidents.
Simultaneously, evaluate the potential consequences of an incident, considering the severity of injuries, possible property damage, and impact on operations.
A risk matrix (or similar tool) is often used to prioritize risks effectively. A risk matrix is a visual tool that plots the likelihood of an event occurring against the severity of its consequences.
Placing each identified risk on the matrix lets you quickly see which risks require immediate attention. Prioritize those with the highest potential for serious harm, typically located in the matrix’s high-likelihood and high-severity quadrant.
Also Read: 10 Best Risk Management Software Solutions for 2025
Step 3: Control and Documentation
Following risk evaluation, implement control measures to mitigate identified risks and meticulously document the process. Control measures may include engineering controls, such as machine guards, administrative controls, safety procedures, or personal protective equipment (PPE).
Implement Control Measures:
- Prioritize the elimination or substitution of hazards before resorting to less effective controls.
- Control measures may include engineering controls, such as machine guards, administrative controls, safety procedures, or personal protective equipment (PPE).
Maintain Thorough Documentation:
- Maintain detailed records of all identified hazards, risk evaluations, and implemented control measures, including assigned responsibilities and action timelines.
- Documentation should be clear, concise, and readily accessible to all relevant personnel.
- Proper documentation allows for tracking of progress, demonstrating compliance, and facilitating future risk assessments.
Step 4: Review and Updates
Safety risk assessments are not static documents; they require regular review and updates. Establish a timeframe for periodic evaluations, such as annually or after significant workplace changes, to ensure ongoing relevance.
To ensure ongoing safety and effectiveness, safety risk assessments must be regularly reviewed and updated.
- Regular reviews are essential for maintaining the effectiveness of safety measures.
- Revise the assessment whenever new equipment, processes, or materials are introduced, or after any incident occurs.
- Changes in regulations or industry best practices should also trigger a review.
To get this right, you’ll need the perfect set of tools and techniques—let’s explore what those look like.
4 Techniques for Effective Risk Assessments
To conduct a thorough and accurate safety risk assessment, it’s important to use the right tools and techniques.
1. Assemble a Competent Assessment Team
A successful risk assessment relies on the expertise of the team. Involve individuals with specific knowledge of the work processes, equipment, and potential hazards to ensure detailed evaluations. Include personnel from different departments, levels, and workers directly involved in the work to gain a well-rounded view of potential risks. Training and certifications in risk assessment methodologies are valuable assets.
2. Select Appropriate Assessment Methods
Choosing the right assessment methods is crucial for obtaining reliable results. Employ qualitative methods (e.g., checklists, brainstorming) for initial assessments, and quantitative methods (e.g., fault tree analysis) for detailed analysis when data is available. The method should be selected based on the complexity of the process and the availability of data.
3. Actively Seek Employee Input
Directly engage with workers through surveys, interviews, or focus groups to identify potential hazards and understand their concerns. Employee input helps to create a sense of ownership in the safety process and provides valuable insights.
4. Prioritize Detailed Analysis
Once you’ve got your finger on the risks, it’s time to take action. Use a combination of methods as needed. For complex or high risk situations use quantitative methods.
Once you’ve got your finger on the risks, it’s time to take action. Here’s how to implement control measures that work.
Implementing and Managing Risk Control Measures
Once risks have been assessed and prioritized, it’s essential to implement and manage effective control measures. This involves developing a clear plan and using practical solutions.
Once risks have been assessed and prioritized, it’s essential to implement and manage effective control measures through a clear plan and practical solutions.
- Develop an Actionable Risk Management Plan:
Clearly outline responsibilities, timelines, and risk control strategies, prioritizing elimination or substitution of hazards before mitigation. This plan should serve as a living document, regularly reviewed and updated to reflect changes in the workplace.
- Implement Engineering and Administrative Controls:
Utilize physical changes to the workplace or equipment (engineering controls) and changes to work procedures or policies (administrative controls) to reduce risks. Consider incorporating employee feedback during the design and implementation of these controls to enhance their effectiveness.
- Provide and Enforce Personal Protective Equipment (PPE):
When other controls are insufficient, provide appropriate PPE and ensure employees are trained on its proper use and maintenance. Regular inspections of PPE should be conducted to ensure it remains in good condition and provides adequate protection.
Enhance Safety Risk Assessment with VComply
VComply’s RiskOps platform significantly enhances the implementation and management of risk control measures. It provides:
- Centralized Control Tracking: Maintain a detailed repository of all implemented controls, linking them directly to identified risks. This ensures clear visibility and accountability.
- Automated Task Management: Assign control implementation tasks, set deadlines, and track progress, ensuring timely execution and reducing manual oversight.
- Real-time Monitoring and Reporting: Gain real-time insights into the effectiveness of implemented controls through dashboards and reports. Identify control gaps and areas requiring further attention.
- Workflow Automation: Automate control-related workflows, such as approval processes and periodic reviews, streamlining operations and improving efficiency.
- Evidence Collection and Audit Trails: Securely store evidence of control implementation and maintain detailed audit trails, facilitating compliance and demonstrating due diligence.
- Integration with Existing Systems: Integrate VComply with existing systems, such as incident management and asset management, to create a unified risk management ecosystem.
- Control Effectiveness Measurement: Utilize the platform’s built-in tools to measure the effectiveness of controls through key risk indicators.
With VComply’s RiskOps platform, you can move beyond manual control management and embrace a more proactive, data-driven approach to risk mitigation.
Final Words
Conducting effective safety risk assessments is vital for maintaining a safe and compliant workplace. By identifying hazards, evaluating risks, and implementing control measures, organizations can significantly reduce workplace accidents and ensure regulatory adherence.
However, managing these tasks manually can be time-consuming and prone to errorsThis is where VComply steps in. With its RiskOps platform, VComply simplifies the entire risk management process. From centralized control tracking to real-time reporting and system integration, you can use these tools to enhance safety risk assessments, improve efficiency, and reduce errors.
Ready to transform your safety practices? Request a demo of VComply today and discover how our solutions can help you create a safer, more compliant workplace.